Onshape is enabling companies like Trek to use CAD in better ways while developing innovative designs for bicycles and accessories. The cloud-native architecture makes CAD and model data more accessible than ever (and more fun, too).
Beyond revolutionary data management capabilities and best-in-class modeling and surfacing tools, Onshape also provides simulation to give engineers feedback on their design decisions as they’re being made.
Learning how to use simulation for design iteration is imperative for engineering students, but it’s not always easy to access and use the software.
The PTC Education team developed a model bike frame design challenge to help educators introduce their students to iterative design using Onshape Simulation.
The Bicycle Frame Design Challenge
Simulation software has traditionally required powerful computers and extensive knowledge to use, making it prohibitive for most educators and students. Onshape Simulation runs in the cloud and is built seamlessly into Assemblies, making it the most accessible way to introduce students to structural simulation.
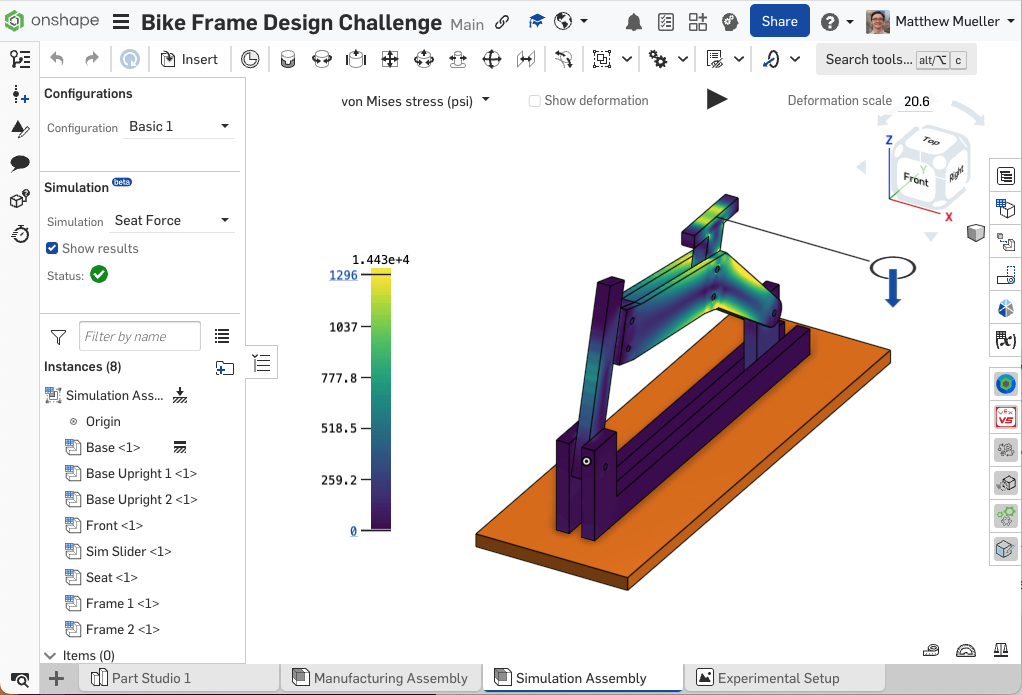
For the design challenge, students are asked to modify the bike frame in this starter Document to achieve a target stress-strain curve (4 mm of deformation at 200 N of force) when fabricated and placed on a force test stand.
You can find more details and a full write-up on how to run the project in the Onshape Learning Center.
To test the design, the laser-cut bike frame parts are connected to a prefabricated rig with a seat and wheel on a force test stand. Automated force test stands costing thousands of dollars would be the most accurate way of measuring the stress-strain curve of a part, but you can add a rotation gauge to a manual force test stand and plot the stress-strain curve for around $250.
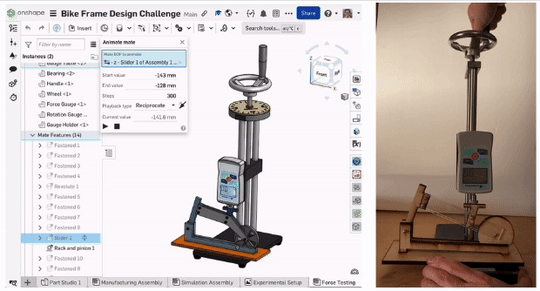
Tufts University Hackathon Takes on the Challenge
We decided to test out the design challenge with 16 students at Tufts University in a two-hour hackathon hosted in their makerspace. The hackathon started with an introduction to the design challenge and the scoring system that turned it into a friendly competition. The score for each design was based on how close they came to the target deformation of 4 mm at 200 N of force, with additional incentives for a lighter-weight frame.
We then tested a couple of provided sample designs on the force test stand. Regardless of how sophisticated a simulation platform is, the results will always be different from experimental results, so these data points were key to providing the students with guidance on how to use Onshape Simulation.
After that, the students were off to the races, modifying the frame to meet the target stress-strain curve. And, of course, there was pizza to help fuel their design iterations.

Some students worked on their own, while others leveraged the collaboration features in Onshape to work together in the same Document. Even students with limited experience using CAD software and simulation were able to participate in the challenge.
Bike Frame Fabrication and Testing
As the students finished their designs, they headed over to the laser cutter to fabricate their bike frames out of acrylic. Seven groups were able to fabricate and test their designs, and three of them were able to complete two rounds of testing.
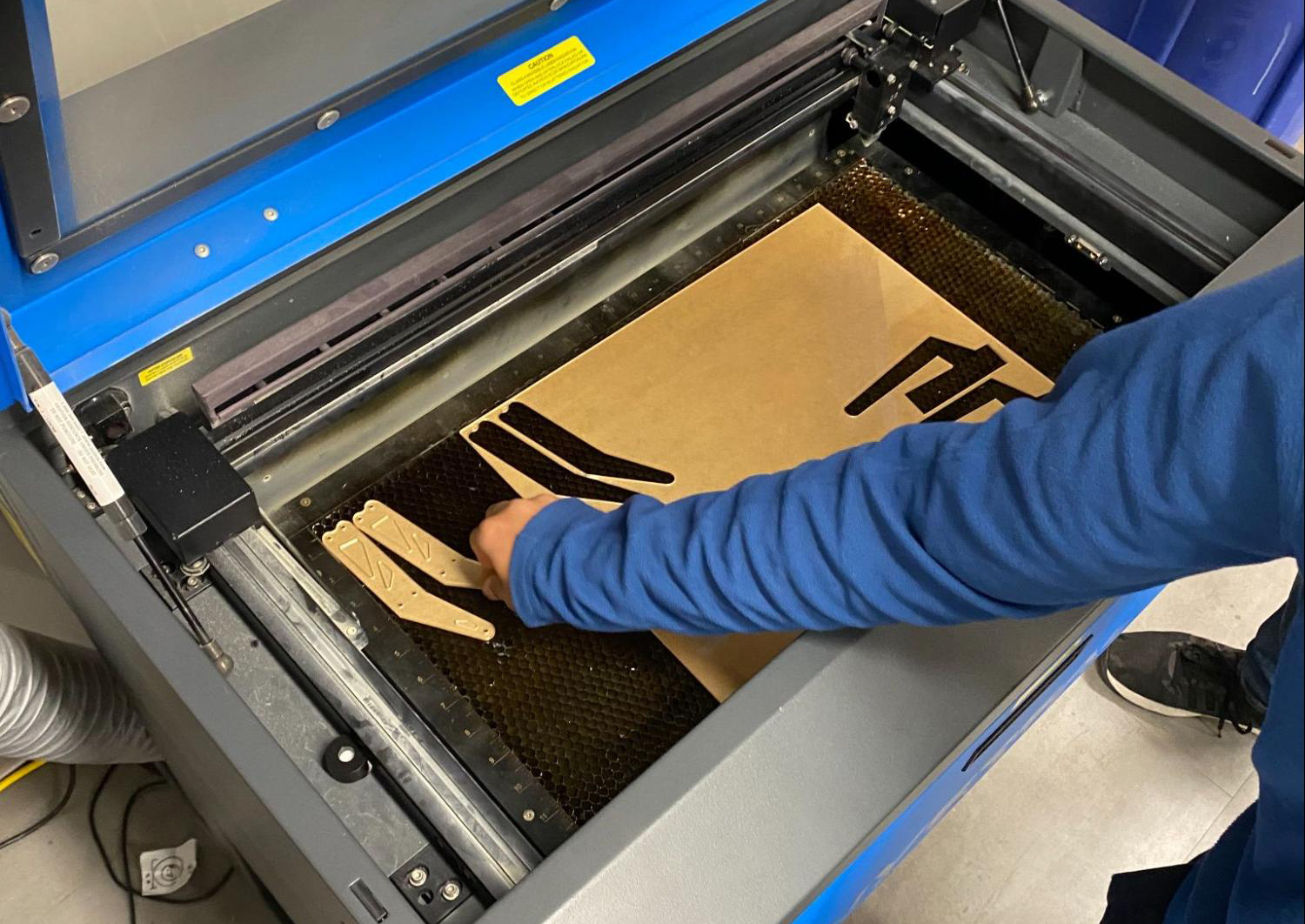
After using Onshape to measure and record the mass of the frame that was cut, the students assembled their bike frame to the test rig and waited their turn to measure the performance on the force test stand.
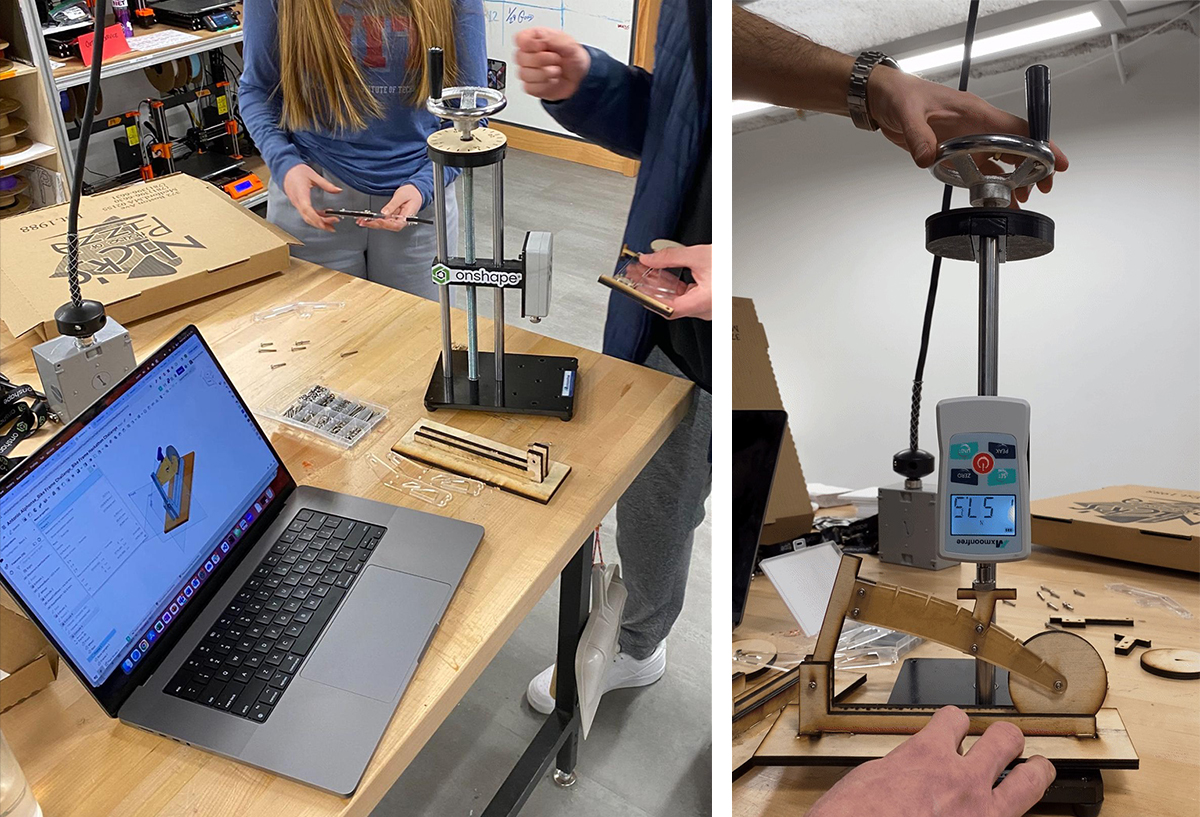
One of the first designs tested by the students was measured to have deformed 4 mm at 195 N of force, just 5 N away from the target of 4 mm of deformation at 200 N. Every other design that the students tested was over 40 N away or 0.5 mm away from the goal, even for the 3 groups that iterated on their design quickly enough to test two designs.
The Buzzer Beater
With only 10 minutes left in the 2-hour hackathon, a student who diligently iterated on her design in Onshape throughout the entire hackathon finally sent it to the laser cutter to be made. She assembled the bike frame and got the design on the force test stand as the clock reached 2 hours since the start of the hackathon.
The design measured 190 N of force at 4 mm of deformation, 5 N farther from the target than the design tested earlier, which was in the lead for most of the hackathon. However, the last frame tested weighed 7 grams, while the earlier design weighed 8.5 grams.
With the incentives in the scoring system for lighter-weight designs, the final design tested came out on top!
Learning Center Projects
Are you looking for inspiration on how to implement project-based learning with your students? Check out this project and many more in the Onshape Learning Center.
But first, sign up for the Educator Plan, which was designed to help teachers get the most out of Onshape’s revolutionary CAD and data management capabilities. The plan includes access to advanced features like Classes & Assignments and Onshape Simulation.
Onshape Educator Plan
Make grading easy with Classes & Assignments.
Leverage Onshape Simulation in the classroom.
Access powerful CAD anywhere, anytime.