Nearly every man-made object on this planet – a machine, computer, phone, tablet or even a bottle of shampoo – is manufactured somehow. You need to design it, create a manufacturing plan, sell and ship it to the customer, provide service parts, and recycle at end-of-life. Imagine the vast amount of critical information needed to make all this happen. That’s where Product Lifecycle Management (PLM) systems come into play.
There are many ways to define PLM, whether it be through the lens of business initiatives, strategy, technology, or software packages. But here’s a good starting point:
PLM is a way to organize and connect all elements of the product lifecycle. It is data about the product and the way to manage it. PLM is a way to organize the data about the product designed by a company, managing changes of the data, and connecting people in various activities such as design, manufacturing planning, sales, support, and maintenance.
How should we move from this formal definition into a more pragmatic way of thinking about PLM? It’s most useful to focus on four aspects of PLM project maturity:
- Vision and Strategy
- Business Execution
- Product and Technology
- Implementation and Data Management
Let’s take a closer look at each element.
1. PLM Vision and Strategy
Everything needs a vision. As an organization, your PLM vision needs to define how digital tools will increase profit, optimize cost, increase quality, and accelerate your speed-to-market. The best PLM vision will lay down a way for a company to run a business using digital tools and leveraging the value of data. This vision must create a comprehensive picture of connecting product information and business silos together, including virtual and physical products.
2. PLM Business Execution
To have a vision and strategy is not enough. Culture is eating vision for breakfast, strategy for lunch, and it stays hungry to ruin your dinner plans. To turn your PLM vision and strategy into reality, you need to have a business execution plan. You need to have measurable criteria for success, and a phased delivery plan that includes people and their organizational responsibilities. Because PLM is a cross-disciplinary initiative, you also must have key company executives committed to the transformation process.
PLM is a process and as a process, it must be measured. This includes all stages of product development, manufacturing, support and maintenance. As part of your transformation process, you need to establish metrics and build Key Performance Indicators (KPIs) to improve them. For example, if you want the Engineering Change Order (ECO) turnaround time to go down, you need to find a way to measure the turnaround time for every ECO.
3. Product and Technology
It is impossible to speak about today’s technology and not start with digital transformation, which is a business imperative for industrial companies and manufacturing. It is important to focus on digital technologies that can make a difference and transform processes holistically. Moving PDF files into a file vault does not make a process digital. The point of digital transformation is to change the entire product design process, how teams communicate, how they make purchase orders and send jobs to contractors. It’s about moving beyond hard copy spreadsheets, uncontrolled documentation, and copied 2D and 3D files shared between thousands of people and tools.
Cloud technology is now driving two important aspects: the ability to deliver products globally, and to introduce a new business model of Software as a Service (SaaS). PLM first leveraged networks, allowing data to be centralized – this was a big step for PLM technologies to focus on a single version of the truth. Then hosted cloud servers made the next step of simplifying access and reducing IT work. Cloud technologies are now redefining PLM by introducing globally available applications that are shared by many companies.
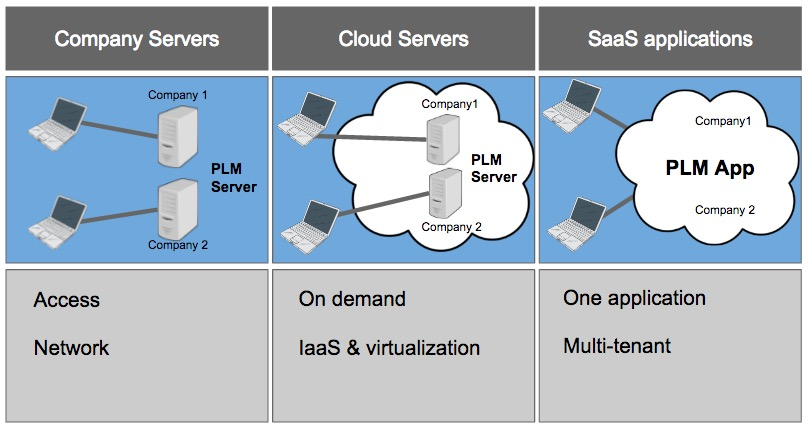
4. Implementation and Data Management
Data and data management are fundamental elements of PLM. They are critical for product design, manufacturing, and support. PLM is focused on solving key manufacturing business problems related to controlling product costs and optimizing business. When 70% of a product cost is defined during the design stage, the reliance on the design data becomes even more important.
Therefore, CAD data management often has a heavy influence on any decisions about how to manage data in PLM systems. At the same time, if a system is locked in the engineering department, the ability to provide a complete view of product cost and process optimization is very limited. Building the connection between design, engineering and the rest of the business is the most challenging piece of a successful PLM implementation.
CAD and PLM
Historically, there are two groups of PLM systems:
- PLM systems with CAD roots.
- CAD-agnostic PLM systems.
Early PLM software was born as a natural extension of the CAD industry. It initially started as just data management for design and engineering, but later evolved to include functions capable of managing product development processes and providing information about the product to downstream processes. Connection to CAD (design) data provided important information to drive the product lifecycle in an organization. However, CAD connections created an additional level of complexity, increasing software dependencies and making it difficult to use outside of engineering.
Meanwhile, CAD-agnostic PLM systems were born independently of CAD vendors. The idea of focusing on product development processes without having deep roots in CAD remains an appealing approach today. In the past, CAD-agnostic PLM suffered from a lack of integration.
Modern cloud services are creating new opportunities by blending both approaches and improving integration between applications and services. The integration between CAD and PLM is becoming easier, and applications are becoming more granular and easier to blend together. Future SaaS CAD and PLM systems will co-exist and be blended in a more unified user experience.
Legacy Data
Legacy data is also an important element of PLM. Managing and importing existing (legacy) data is a complicated, time-consuming and very expensive task. It can easily cut into your implementation budget and increase project time.
The legacy data issue is not limited to the PLM domain. Tackling business intelligence and legacy systems are top priorities for a CIO. Legacy data is the information stuffed in filing cabinets and Excel spreadsheets, or buried in antiquated data management systems, whether they be company-built or acquired over the last two decades. These systems are sitting in corporate data centers or sometimes under the desks of employees.
Collaboration
Collaboration is a very generic word. But it is often used by PLM systems to explain the nature of the communication process happening between people, departments, organizations, service providers and customers. A PLM system’s collaboration tools improve data sharing, process flow, and control.
What’s the Difference Between PDM and PLM?
People often confuse PDM (Product Data Management) and PLM (Product Lifecycle Management). In my view, PDM is about technology and products, helping companies take control of their 3D CAD files (storage, revisions, and lifecycle). PLM is a more holistic approach to data and process management, including Bill of Materials (BoMs) Management, Change Processes, Portfolio and Product Management, Quality Control, Maintenance and Support, and many other critical functions.
PDM functionalities are now becoming available as online services, managing design information that can be easily included in upstream-downstream process scenarios. The future will bring even more granular services and I expect that the border between PDM and PLM will eventually disappear.
Why Will the Future of Digital PLM be Different?
The previous generation of PLM systems were designed on top of an SQL database, installed on company premises to control and manage company data. It was a single version of truth paradigm. Things are changing and the truth is now distributed. It is not located in a single database in a single company. It lives in multiple places and it updates all the time. The pace of business is always getting faster. To support such an environment, companies need to move onto different types of systems – ones that are global, online, optimized to use information coming from multiple sources, and capable of interacting in real time.
Isolated SQL-based architectures running in a single company are a thing of the past. SaaS is making the PLM upgrade problem irrelevant, as everyone is running on the same version of the same software. Furthermore, the cost of systems can be optimized and SaaS systems can serve small and medium-size companies with the same efficiency as large ones.
Although PLM might sound like a complex discipline, it is actually the most effective way to run your business. Go with small steps and remember, Product Lifecycle Management never ends. Your products and processes can always get better.